Home >
Artificial Rock Sculpting Tutorial
Artificial Rock Sculpting - Practice Makes Perfect
The art of sculpting takes patience and practice to achieve professional results; however a few basic guidelines will ensure that you produce results strikingly similar to naturally occurring stone even on your first attempt.
For beginners it is recommend to start simple, and you will almost certainly be pleased with the outcome. Take the knowledge that you will gain in working with the concrete this time and use it when building the form for your next project. As a guideline, the simpler your rock is, the more like natural stone it will appear in the end product. This is true only until you have mastered the ability to sculpt the intricate and predictable patterns in naturally occurring stone by hand and eye.
There is no real substitute for a solid understanding of the principals and formations of naturally occurring rock formations, however you may find that you can 'cheat' the process a little. Using a texture mat made from taking an impression of real rock you can re-create naturally occurring detail with remarkable ease and effect. Texture mats can be in any size or shape and can consist of a general texture pattern, or a combination of general texture as well as a pronounced crack or fissure. On larger projects you can lay the pattern of the pronounced crack in the texture mat from end to end. This will allow you to create long and dramatic runs of fault lines in the rock.
Pictures of the texture mat process are included with the sculpting instruction below.
Mix enough concrete to cover at least half of your rock before you start
You should pre-make enough concrete to cover at least half of the project at hand. If you anticipate needing quite a few batches of the concrete you may like to make the initial few batches JUST A TINY BIT on the wet side so that they will be readily workable by the time you get back to them.
Below is a comparison to help you find the correct moisture level for your concrete. Take a handful of concrete and try to form a ball in your hand. The pictures below detail too wet, too dry, and just right.
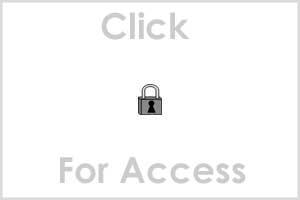
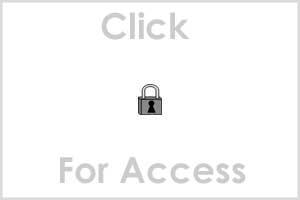
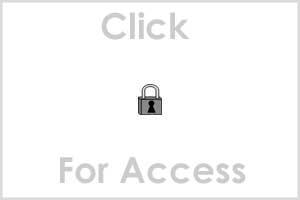
Once you have a few loads of mixed concrete at the ready you are going to begin applying the concrete to your form. It is recommend to place your form on clean and level surface with plenty of light and space on all sides. Building on a suitably sized piece of plywood will allow you to transport the rock earlier than if it must support its own weight. Cover the entire work are underneath with poly sheets or any kind of durable tarp or plastic. Sculpting concrete is messy business and be certain that concrete can ruin many different surfaces so keep your work area as clean as possible.
Place large handful of concrete at four separate corners of your form. This will help to anchor it in place as you will be applying the concrete to your form with a small amount of force. You need to ensure that it will not slide shake or move too much or you will inevitably have the concrete collapse and fall off in big sections.
When you apply the concrete you will do so from the bottom up. Take small handfuls of concrete and place it at the base of the form with enough thrust to cause it to splatter out slightly when it hits the target. What you are trying to do is to avoid any pockets of trapped air, and also ensure that the concrete wraps right around the steel grid work or your form. Do not use your point trowel at this stage for anything other than tamping in slightly areas of thrown concrete that look like they want to fall away from the side of your form.
Continue throwing handfuls of concrete all around the base of your form until you have completed a perimeter pass of your form. You will repeat this process of adding 2-4 inches of height for every complete pass around the form of concrete as you slowly build the concrete up towards to top of your rock. Very quickly you will see a picture forming of how much concrete you are going to need to complete the project.
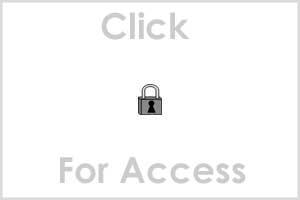
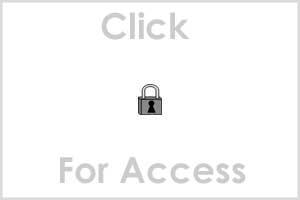
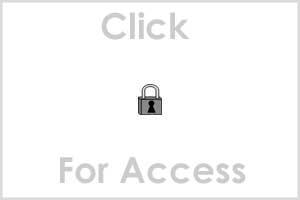
NOTE: The concrete should have the tendency to tenaciously cling onto the criss-crossing of the steel skeleton as you gently lob it into place. Vertical slopes of 90 degrees or more can be very tricky and sometimes can require a second application of concrete after the first has partially cured so try to keep vertical climbs at a minimum while you are learning these skills.
You should now start to have a feel for how much more concrete, if any, you will require to cover the basic structure of your form. It is important to thoroughly cover your entire rock with concrete before any real sculpting begins. You want the stone to have uniform strength when the concrete dries so it is best so work diligently to get the entire structure buried in concrete with enough time left to spare to take a quick breather and get back to work at sculpting.
Your comfort with the working times of concrete will increase with experience.
The artificial rock hand sculpting process
Using a perfectly clean point trowel you will begin the process of dipping the trowel in fresh clean water and smoothing out the concrete always in the motion from bottom to top. The concrete is clinging to the steel structure of your form and a soft touch is required to ensure that you do not send slumps of concrete falling down while you are working at smoothing it out.
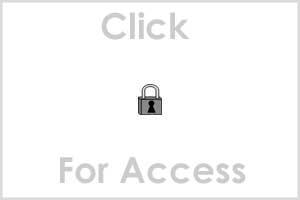
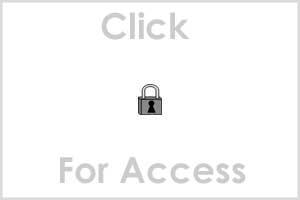
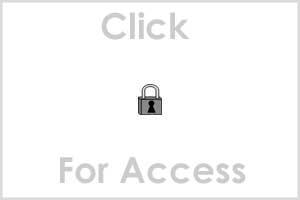
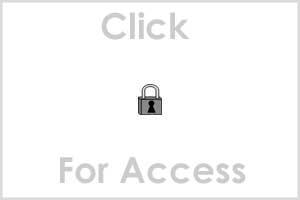
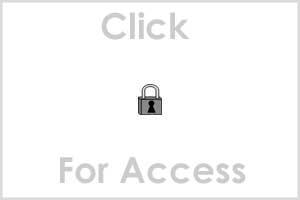
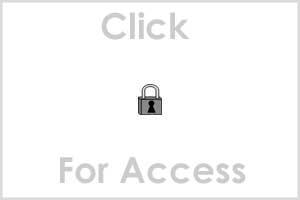
Once you have covered your form in concrete and the total structure seems to be stable you can begin the detail sculpting process. It is critically important that you have even coverage of concrete over your form to ensure strength in the end result.